Plastic extrusion for optimized, flexible manufacturing solutions
Plastic extrusion for optimized, flexible manufacturing solutions
Blog Article
A Comprehensive Guide to the Process and Benefits of Plastic Extrusion
In the vast world of manufacturing, plastic extrusion arises as a essential and highly reliable procedure. Transmuting raw plastic right into constant profiles, it provides to a huge selection of sectors with its amazing versatility.
Comprehending the Essentials of Plastic Extrusion
While it may appear facility at first glance, the procedure of plastic extrusion is essentially simple. The procedure begins with the feeding of plastic material, in the kind of granules, powders, or pellets, into a heated barrel. The shaped plastic is then cooled, strengthened, and reduced into wanted lengths, completing the process.
The Technical Process of Plastic Extrusion Explained
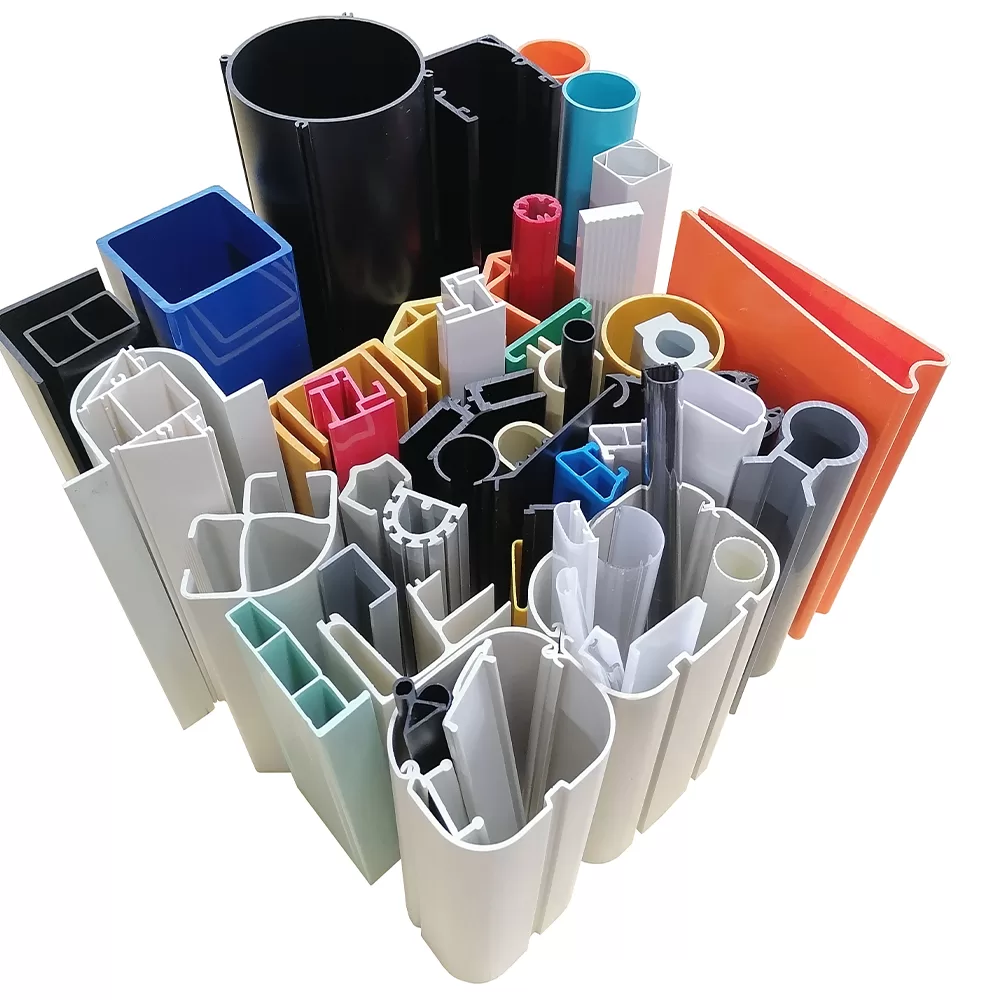
Sorts Of Plastic Suitable for Extrusion
The option of the right kind of plastic is an important facet of the extrusion process. Different plastics provide one-of-a-kind homes, making them a lot more fit to particular applications. Polyethylene, for instance, is commonly made use of due to its reduced price and easy formability. It supplies superb resistance to chemicals and moisture, making it perfect for items like tubing and containers. Similarly, polypropylene is one more popular selection due to its high melting factor and resistance to tiredness. For even more durable applications, polystyrene and PVC (polyvinyl chloride) are often picked for their toughness and longevity. These are usual options, the choice ultimately depends on the certain needs of the product being produced. Recognizing these plastic types can considerably boost the extrusion procedure.
Contrasting Plastic Extrusion to Other Plastic Forming Approaches
Understanding the sorts of plastic suitable for extrusion paves the method for a more comprehensive discussion on exactly how plastic extrusion stacks up versus various other plastic creating methods. These consist of shot molding, strike molding, and thermoforming. Each approach has its distinct usages and advantages. Shot molding, as an example, is excellent for creating detailed parts, while strike molding is perfect for hollow things like containers. Thermoforming excels at forming huge or superficial parts. Nevertheless, plastic extrusion is unequaled when it pertains to developing continuous accounts, such as seals, pipelines, and gaskets. It also permits a regular cross-section along the size of the item. Hence, the choice of approach mostly depends upon the end-product requirements and requirements.
Secret Advantages of Plastic Extrusion in Manufacturing
In the realm of manufacturing, plastic extrusion provides numerous substantial benefits. One remarkable benefit is the cost-effectiveness of the procedure, that makes it a financially appealing manufacturing approach. In addition, this method supplies premium product adaptability and enhanced production rate, thus boosting total production efficiency.
Cost-Effective Manufacturing Approach
Plastic extrusion jumps to the leading edge as a cost-efficient manufacturing method in manufacturing. This process sticks out for its capacity to generate high quantities of material swiftly and efficiently, providing makers with considerable savings. The key expense advantage is the capacity to use less costly basic materials. Extrusion uses thermoplastic materials, which are less costly compared to ceramics or metals. Even more, the extrusion procedure itself is relatively simple, decreasing labor costs. In addition, plastic extrusion calls for less power than traditional manufacturing methods, adding to lower operational expenses. The procedure likewise minimizes waste, as any excess or faulty products can be recycled and recycled, supplying another layer of cost-effectiveness. Overall, the monetary benefits make plastic extrusion an extremely attractive alternative in the production sector.
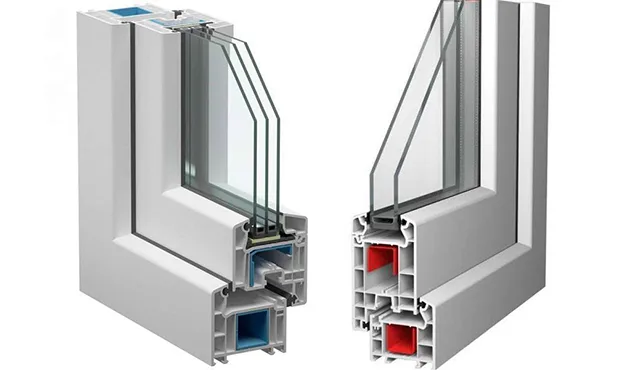
Superior Product Versatility
Past the cost-effectiveness of plastic extrusion, an additional considerable advantage in making lies in its superior product flexibility. This process enables the development of a large selection of items with varying forms, styles, and sizes, from simple plastic sheets to intricate accounts. The adaptability is connected to the extrusion die, which can be tailored to yield the desired product layout. This makes plastic extrusion an ideal remedy for sectors that need personalized plastic parts, such as automotive, construction, and packaging. The capacity to produce diverse items is not only advantageous in conference details market demands however likewise in making it possible for manufacturers to check out new line of product with minimal capital expense. In significance, plastic extrusion's item flexibility cultivates technology while improving functional efficiency.
Enhanced Manufacturing Rate
A substantial advantage of plastic extrusion exists in its improved production rate. Couple browse around this web-site of various other production procedures can match the speed of plastic extrusion. In addition, the capability to maintain consistent high-speed production without sacrificing item top quality sets plastic extrusion apart from various other techniques.
Real-world Applications and Impacts of Plastic Extrusion
In the world of production, the method of plastic extrusion holds profound importance. The financial advantage of plastic extrusion, mostly its high-volume and affordable outcome, has actually changed production. The industry is constantly striving for developments in biodegradable and recyclable materials, suggesting a future where the advantages of plastic extrusion can be preserved without endangering environmental sustainability.
Conclusion
To conclude, plastic extrusion is a highly reliable and efficient technique of transforming raw products into varied products. It uses countless benefits over various other plastic developing approaches, consisting of cost-effectiveness, high output, very little waste, and layout adaptability. Its influence is greatly felt in different markets such as building and construction, auto, and customer items, making it a pivotal procedure in today's manufacturing landscape.
Diving deeper into the technical process of plastic extrusion, it begins with the choice of the suitable plastic product. As soon as cooled down, the plastic is reduced right into the needed lengths or injury onto reels if the item is a plastic movie or sheet - plastic extrusion. Comparing Plastic Extrusion to Various Other Plastic Forming Methods
Recognizing the types of plastic appropriate for anchor extrusion paves the method for a more comprehensive conversation on just how plastic extrusion stacks his comment is here up against other plastic forming approaches. Few various other production processes can match the speed of plastic extrusion.
Report this page